When prototyping quickly and rehearsing with performers to test out different sensor placement set-ups, I do not always have time to create whole sensor garments.
I learned about this kinesiolosgy tape from a fried who had a muscle injury. The tape is made so that by taping on body directly it supports and massages muscle. What is interesting about this tape is that it is very stretchy on one direction (length) but not on the other (width), and is made out of textile material. You can buy it at local drugstores. I tried out few different types of construction with conductive fabric, threads and resistive fabric to make pressure/bend sensor with this tape.
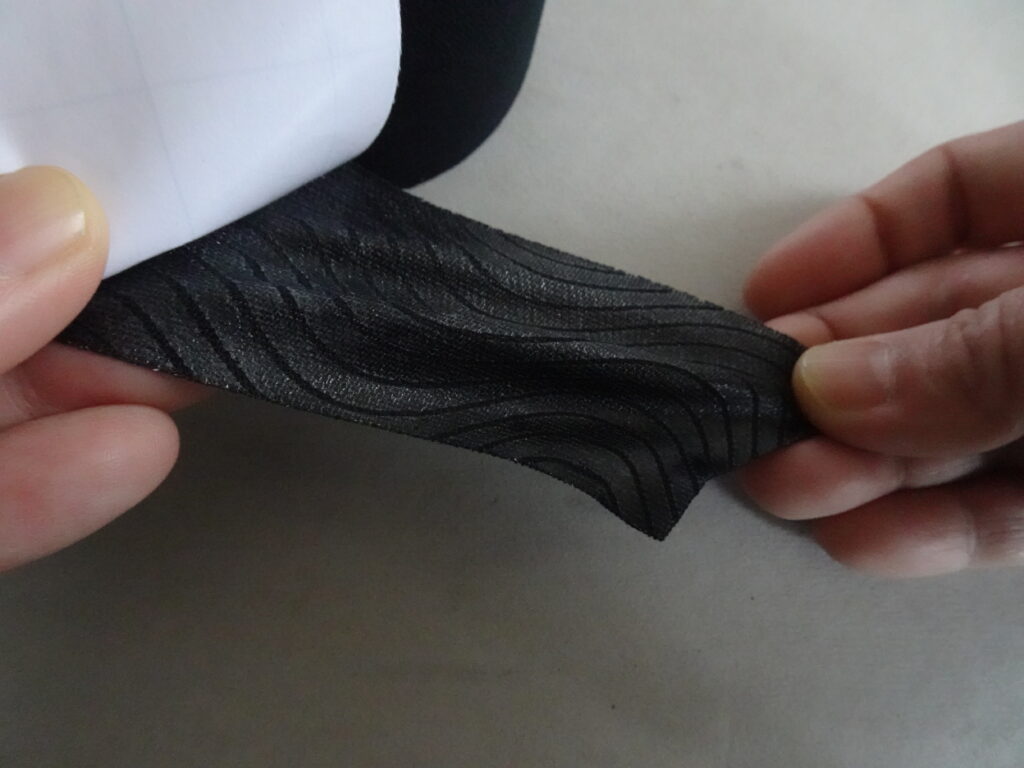
The result is quick to make, very flexible and stretchy tape like sensor that is suitable to stick on body parts, directly on skin or on garments.
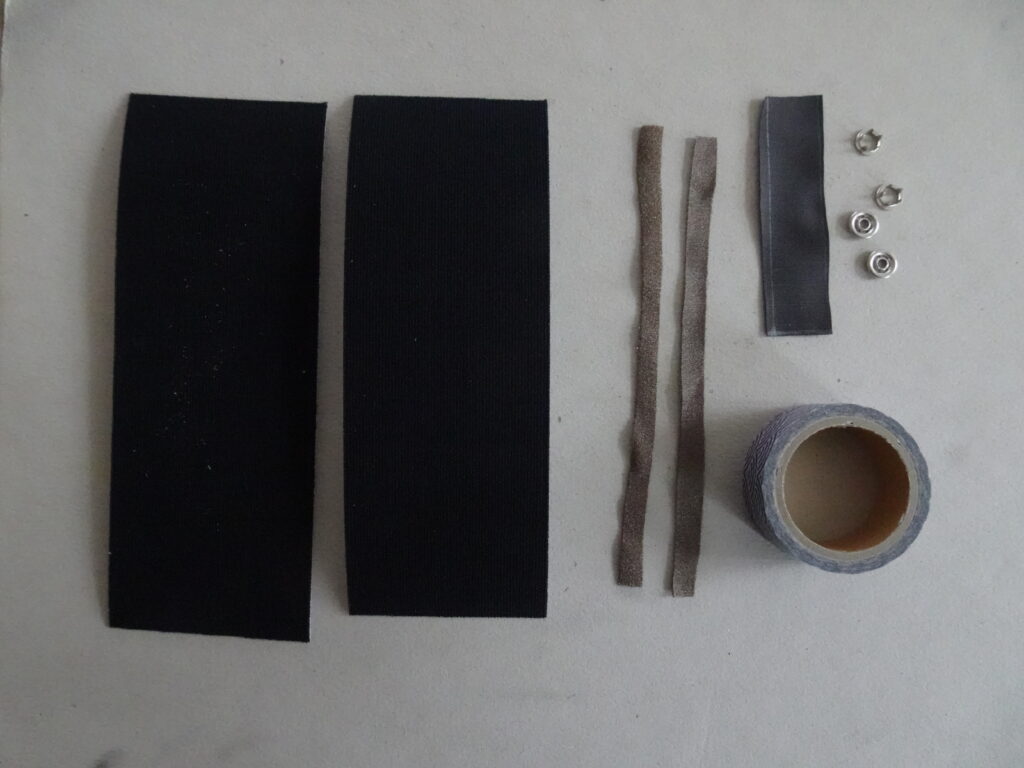
The basic material is above. 2 pieces of kenesiology tape, 2 long strip of stretch conductive fabric (stretch one is better if you want the sensor to be stretchy), eeonyx stretch fabric. In this example I used 7mm snaps to create a connection to fabric cables. You can use other method of connection if you do not have snaps. and lastly some kind of sticky tape to fix the kinesiology tape on your work surface while working. This makes it easier to work with it.
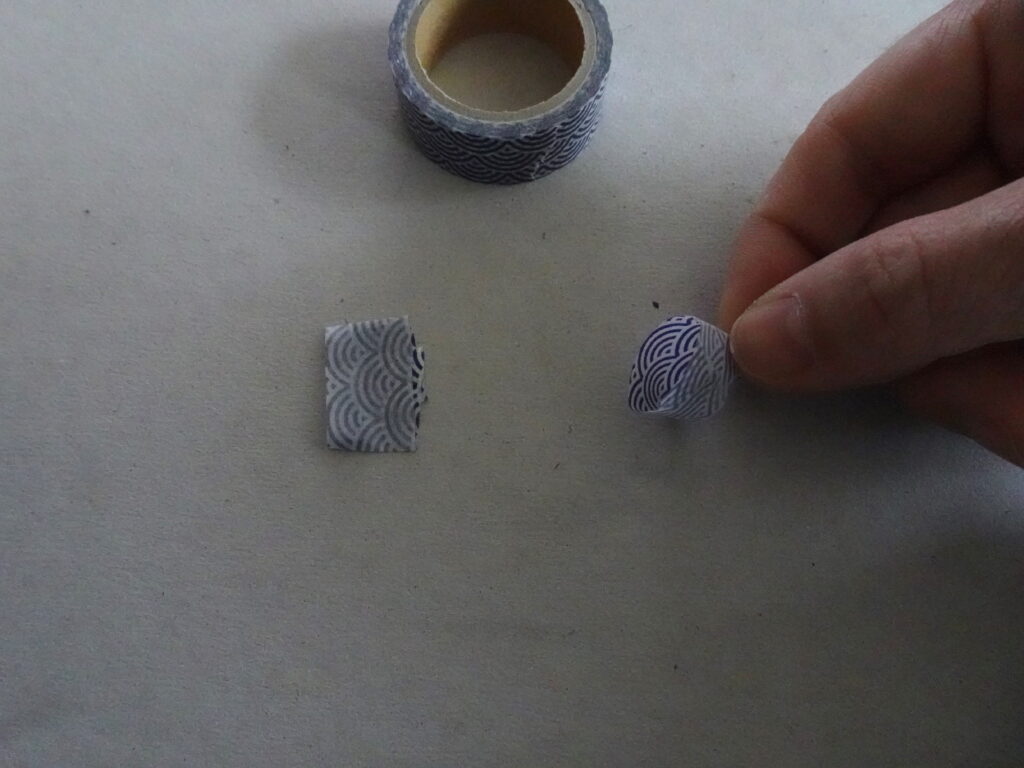
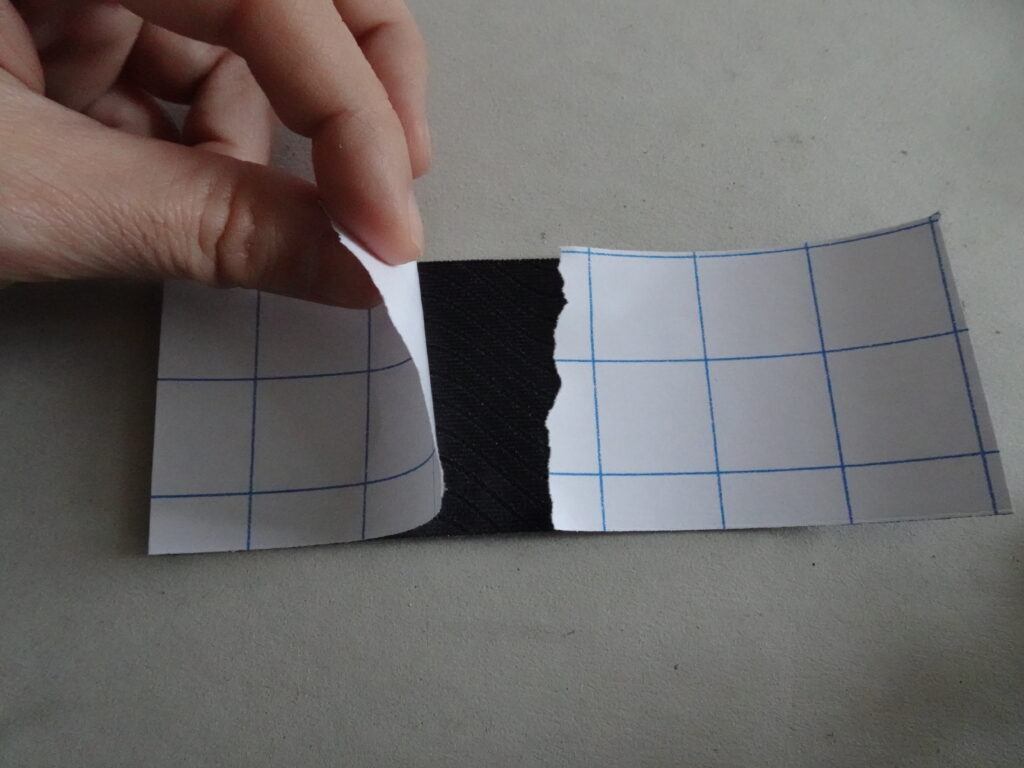
Stick any sticky tape in ring shape onto your work surface and stick the non sticky side of the kinesiology tape so it is fixed on your work surface with sticky side up. Remove the backing paper from the kinesiology tape.
Place 2 stretch conductive fabric strip on the tape. Make sure they do not touch each other. The gap should be narrower than the resistive fabric piece. Then place the eeonyx resistive fabric on them. Make sure that resistive fabric touches both of the conductive strip. Electricity should flow through the resistive fabric between the two strip.
Peel off half of the second kinesiology tape’s backing paper and stick it on the layer just created with the sticky side down. Both of the tapes sticky side should be facing to each other. The outer side is both non-sticky side of the tape.
Trim down the shape of the tape to your desired shape. As I later want to stick them on skin with the same width kinesiology tape, I trim the sensor narrower. The edge is curved so it is easier to remove from the tape after the use.
The above is another design. It is easy to come up with different shapes and cut it as you like. You can to keep in mind that the sensitive point is where the resistive fabric is placed and not the whole tape.
Mark where you want to place the connector and press the snap. The sensor does not have polarity as it is a piece of resistive material. You can use any combination of snap directions (in above example, I used two 凹 snaps) . It is probably a good idea to keep some consistence rules when you make sensors or fabric circuit that uses same kind of snap press so they are interchangeable.
As I want to stick them directly on skin, I cover the back side of the snap with extra tape. This way none of the conductors are touching the skin directly.
You can connect fabric cables that has snap ends to connect this sensor with other components.
The resulting function is similar to other types of fabric bend sensors made of resistive fabrics. When you change the gap with of the conductor, thickness of the conductor strips or size of the resistive fabric, it will change the reading range. It has also quite a bit of wear and tear as you use them. The range tend get smaller and lower resistance.
When you do not have snap/popper, you can also stitch the connection between the conductive fabric and conductive thread. Leave the end of the conductive fabric longer than the tape so it is exposed. Thread a needle with conductive thread, let it go through the paracord to isolate, then stitch one of the conductive fabric to make the connection. After the electrical connection is made, tape the stitched part so it does not come loose. You can add the pins or header on the other end of the thread to connect with breadboard. The detail of how to build this is at the end of this post.
https://www.kobakant.at/DIY/wp-content/uploads/2021/01/DSC00826-300x225.jpg 300w, https://www.kobakant.at/DIY/wp-content/uploads/2021/01/DSC00826-768x576.jpg 768w, https://www.kobakant.at/DIY/wp-content/uploads/2021/01/DSC00826-1536x1152.jpg 1536w, https://www.kobakant.at/DIY/wp-content/uploads/2021/01/DSC00826-2048x1536.jpg 2048w" sizes="(max-width: 1024px) 100vw, 1024px" />
You can also make the sensor using conductive thread as conductor inside the sensor and directly thread through the fabric cable. This way, you can skip the snap connector and make the sensor even smaller.
Cut two pieces of conductive thread. The length of the thread is a size of the sensor + length of the cable. Place it parallel on the kinesiology tape and place the resistive fabric on them. Make sure that resistive fabric touches both of the thread.
Cut another piece of kinesiology tape, slightly shorter than the first piece. Stick it on the layered piece with sticky side down. Flip the long pits up so the thread does not come out from the edge. Trip the shape as you like.
Pull the middle thread from the para cord, thread the needle with the conductive thread coming out from the sensor and let it go through the paracord.
Tape the joint to make sure the paracord does not come off easily. You can use crocodile clip directly on the conductive thread to connect to the sensor.
But if you are prototyping with this sensor, thread is not breadboard friendly. here is one example of how you can use them with breadboard: by using dress pins as connectors.
Make an adjustable loop at the end of the conductive thread, where you want to connect to a dress pin. Place the head of a dress pin in a loop and reduce the size of the loop by pulling the thread.
Add extra loops, and pull to tighten it. This is similar to how you cast on when you knit. I do it 2 times.
Then knot one end of the thread to the other so it does not open. Trip the extra length of the thread. Below video shows the knot made with big yarn so you can see it better.
Add to the joints so it does not slide off from the needle. You can stick the needle to the breadboard. Of course the pin is sharp. Make sure you do not poke yourself by mistake!
Alternatively you can solder the conductive thread to header to make the proper connections. The example on this picture is soldered and the joints are covered with black hot glue so the paracord does not slide off. The dress pin example above is useful when you do not have access to soldering iron.
You can tape the sensor on skin with another piece of kinesiology tape. This way you can quickly test different sensor positions. For example, placing a sensor on palm side of the joint or knuckle side of the joint makes a difference in readings and overall sensor behavior. You can see which side captures your desired movement.
You can also use skin glue to glue the sensor directly on the skin. I used cosmetic glue for fake eye lashes to glue the sensor on skin and applied tape over it. This way the sensor moves as your skin moves and captures even subtle moves.
One can make it also directly on the tape and tape it on body… but this way one has to discard the sensor (which include a lot of conductive material inside) for every use, which I really do not want to recommend. Instead, the sensor itself is not sticky, but you can use other tape or skin glue to place on the body and reuse it.
Leave a comment